A steady stream of the curious have passed by the Miniota, Man., farm of Don and Ken Armitage since they started harvest Aug. 20.
Around Milden, Sask., locals are keeping an eye on what happens in Ian McPhadden’s fields.
The farms are the first to take possession of the machines that aim to beat the combine at its own game, the McLeod harvest system.
The system includes a pull-type harvester that collects chaff and weed seeds along with grain, leaving only straw behind on the field. An automated stationery cleaning mill separates the grain from the crushed residue, which becomes livestock feed.
Read Also
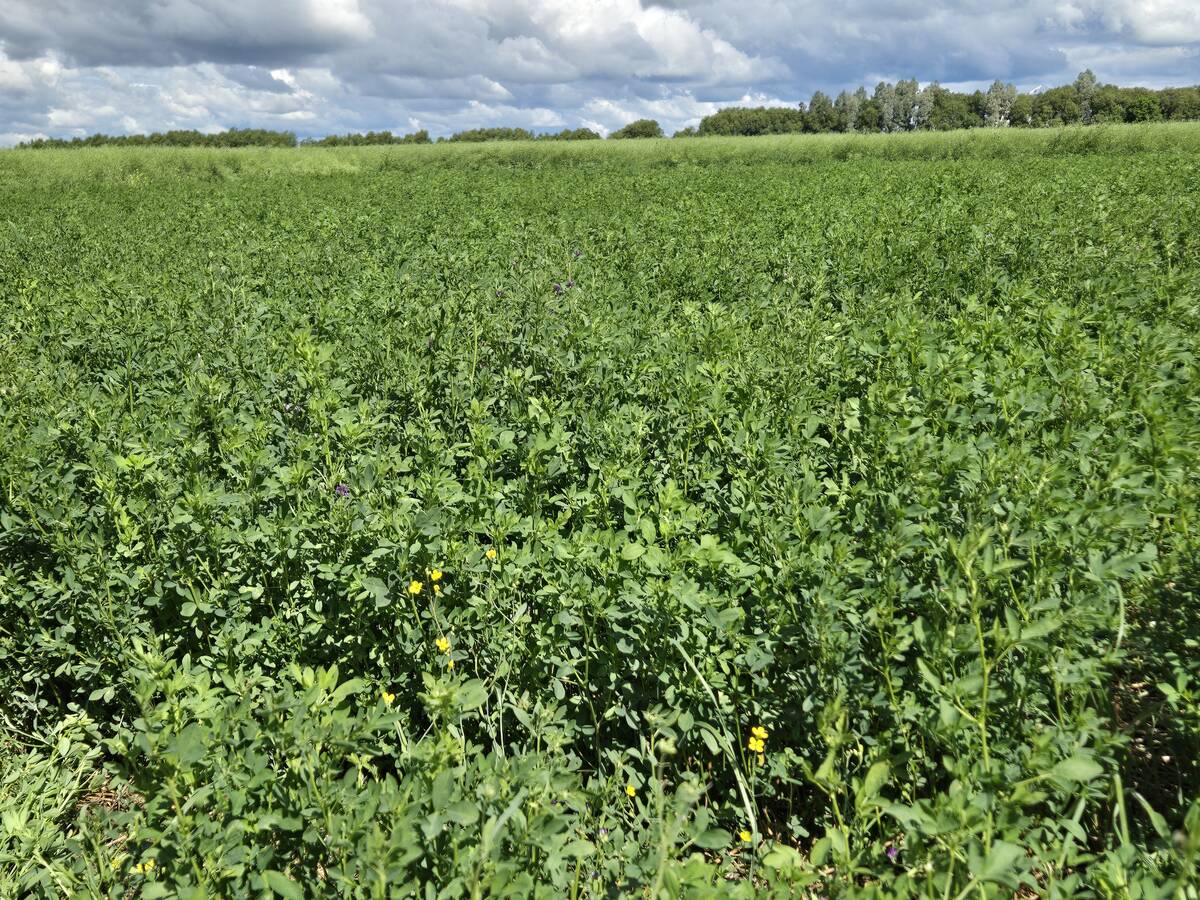
Manitoba Parkland research station grapples with dry year
Drought conditions in northwestern Manitoba have forced researchers at the Parkland Crop Diversification Foundation to terminate some projects and reseed others.
The farmers are committed to working with McLeod on his research, but they aren’t scrapping their traditional combines just yet.
Don Armitage is eager to pioneer the unique field harvester and stationary cleaning mill.
“In another way, it makes a person a little nervous, too,” noted Armitage.
However, indefatigable entrepreneur Bob McLeod and his crew have given the farmers a kid-gloves service agreement.
McLeod has promised his crew will be close by to fix problems and will take the equipment back this winter to work out any bugs.
A year ago, McLeod had hoped he would be producing the system commercially for the 2001 harvest.
But he said his team has since decided to slow things down to ensure the equipment works perfectly. Next summer, he hopes to have several more farmers like Armitage and McPhadden using the system.
Armitage was impressed by the potential of McLeod’s concept when he first heard about it in 1994, and has followed the invention’s progress since.
“I’ve known there’s a big feed source going to waste in the form of chaff, so this was a way of capturing that.”
Research done by University of Manitoba economists estimates the value of the feed at $17 per acre.
For Armitage, a cow-calf producer, the new source of feed means he won’t have to bale as much hay.
“We were trying to figure out how we could make our cropping more profitable and this seemed like the best way to do it,” said Armitage.
If all goes well, Armitage plans to take off 700 to 800 acres of barley, wheat, lentils, flax, canola and mustard with his system.
So far, he said the mill has been working well but the harvester still needs some capacity improvements.
The harvester’s tank needs to empty faster, said Armitage, and he thinks the elevating augers could be larger.
Intriguing concept
Like Armitage, Ian McPhadden was intrigued by what he had read about the McLeod system, and wanted to “look outside the box” and give it a try.
He liked the thought of control ling volunteer cereals in pulse crop rotations and reducing chemical costs by getting rid of weed seeds mechanically.
The University of Manitoba researchers estimate the value of removing weed seeds from the field is $16 per acre.
But what sold him on testing the system was meeting the people involved and examining McLeod’s business plan.
“Most farmers are ga-ga over iron,” said McPhadden, explaining his cautious approach.
“I looked for the business aspect, the management aspect as opposed to the metal aspect of the company.”
In an Aug. 30 interview, McPhadden said he isn’t hanging his hat on the system until he sees it in action.
“There’s a big leap of faith between concept and reality,” said McPhadden.
He took delivery of the equipment last week, and hopes to use it for half his 5,000 acres of lentils, chickpeas, durum, wheat, barley and canola.
He wants to combine the north half of every field with his conventional Klaas combine and use the McLeod harvester for the south half.
That way, after a couple of years, McPhadden will be able to see what impact the McLeod system has on weed pressure.
University of Manitoba researcher Gary Martens will also be on his farm this fall to measure weed seeds and cracked grain left behind by the two harvesting methods.
Since the McLeod system takes more material off the field, McPhadden plans to monitor trucking costs and ground speed.
He also will have to spend some time figuring out whether he gets better returns from marketing the milled chaff and weed seeds to cattle producers, or buying some cattle of his own to add value to the millings.
McPhadden had to upgrade to 400-amp electrical service in his yard for the McLeod cleaning mill, add some extra hopper bins, and buy a header for the harvester.
But he said his agreement with McLeod makes him feel comfortable with the risk.
“This machine is not going to cost me a whole lot of money if it
doesn’t work,” he said.
For more information about the McLeod Harvest system, and dates for field demonstrations, see the company’s website www.mcleodharvest.com.